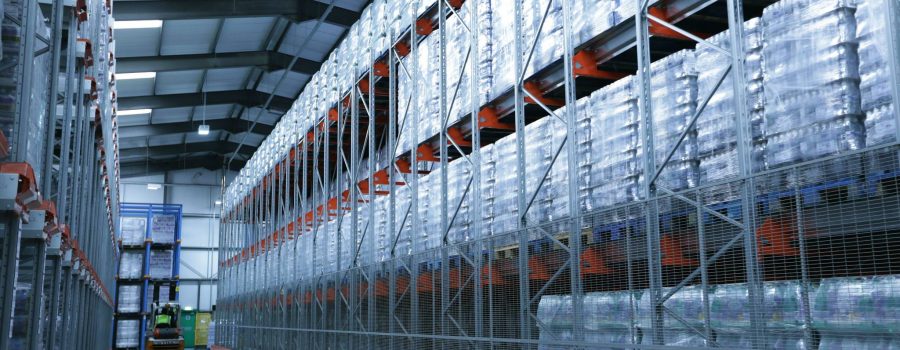
As more and more companies look to Max the Cube by maximising capacity and improving the space utilisation of every inch of the warehouse, the demand for Thistle Systems Maxicube Shuttle Racking, or radio shuttle racking as it is sometimes referred to, is increasing dramatically.
What Is Shuttle Racking
Shuttle racking uses a combination of high-density pallet racking and a semi-automated shuttle device that runs on rails below the beam level and can pick up a pallet and move it along the rails. The shuttle carrier can either despatch pallets into the racking system or retrieve them from the racking and present them at the end of the lane, ready to be collected by the forklift.
Key Benefits of Shuttle Racking
• Increased Capacity from Shuttle Racking
By designing large blocks of high-density racking with virtually zero aisles, you can dramatically increase the number of pallet positions over systems such as APR, push back racking and drive-in racking.
• Improved Space Utilisation
One of the major benefits offered by shuttle racking is the ability to improve space utilisation. This is achieved by a thorough understanding of the SKUs stored, their velocity and using the shuttle to continually move pallets to optimise capacity
• Reduced Forklift Travel Times
As the shuttle carrier does most of the work taking the pallet into or retrieving it from the racking system, the distances travelled by forklifts are significantly reduced.
• Faster Loading Times
The direct benefit of reduced forklift travel times is that it enables pallets to be loaded onto wagons or into the system much faster than other systems.
• Increased Pay Loads Per Operator Per Day
Reduced forklift travel times and faster loading times also enables forklift operators to dramatically increase the number of pay loads per day. Therefore, the solution will likely require fewer forklifts and operators, which can be deployed elsewhere in the organisation – delivering significant cost savings to the warehouse operations.
• Reduced Damage to Racking
Unlike Drive-In Racking, where the forklift has to enter the racking system, the shuttle racking approach reduces the likely contact with the racking structure and so dramatically reduces the likelihood of damage.
Damaged racking can not only be costly and dangerous, but it can also cause significant operational challenges for a warehouse. By reducing damage to racking, warehouses can become safer, more efficient and less costly to run.
• Reduced Damage to Stored Products
The shuttle racking solution reduces the likelihood of damage to products in 2 ways. Firstly, as the shuttle carrier moves the pallet with the goods in the racking, we reduce the manual handling element and, therefore, the likelihood of collisions.
Secondly, the reduced damage to the racking structure also reduces the possibility of collapses and, therefore, damage to the goods.
• Improved Safety in the Warehouse
Safety is a major priority in every warehouse. Reducing travel times and requiring fewer forklifts will automatically reduce the likelihood of accidents. Similarly, the reduced likelihood of damage to racking will also reduce the risk of collapses and potential safety issues.
• Potential to reduce energy consumption and CO2 emissions
Depending on the design and layout of the shuttle racking system, particularly with deep blocks of racking, there may be the opportunity to reduce the amount of lighting in the warehouse to focus it on purely working areas.
Combined with the reduction in the number of forklifts required, shuttle racking should be able to provide ongoing energy savings.
How Can Shuttle Racking Be Used?
• First in Last Out (FILO)
• First in First Out (FIFO)
• Picking Tunnels
• Despatch Areas
Shuttle racking can transform the warehouse’s performance and capacity, particularly with First in Last Out (FILO) and First in First Out (FIFO) systems.
The ability to create storage lanes of up to 100 pallets deep transforms the potential storage capacity of any warehouse using a FILO or FIFO system.
And with the shuttle carriers doing all of the work once the pallet is in the racking system, there are significant performance benefits with reduced travel times and maintenance issues.
However, shuttle racking solutions can also transform the performance of Despatch Areas which often act as a key performance indicator of the overall efficiency of the warehouse.
By incorporating a radio shuttle system over a mezzanine, companies can minimise waiting and loading times by creating dedicated areas with pre-prepared pallets ready to be loaded onto the wagon.