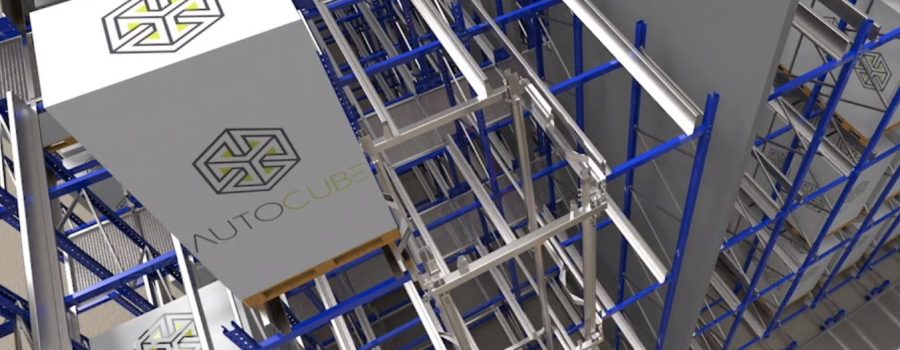
Welcome to the third part of our series on the myths associated with Automated Racking and Automated Storage Solutions.
We have already discussed the myths surrounding the costs of automated storage solutions and automated storage being seen to be only suitable for large warehouses and large cold stores.
One of the biggest concerns we get from customers when developing concept designs and project plans for Automated Storage Solutions is regarding breakdowns.
With such a reliance on equipment and technology, breakdowns are a genuine concern; however, it is one that can be addressed through effective system design.
In every Automated Storage System we design, we look to build in an agreed level of redundancy, which would allow operations to continue to meet specific performance levels in the unlikely event that a component became unresponsive.
We work closely with you to understand the average and peak levels of throughput and design a system that can cope with a breakdown.
So, instead of only having one lift to feed all levels, we would always feature two lifts as an absolute minimum. Similarly, if the peak level of throughput requires six smart carriers, we would definitely incorporate an extra carrier, to allow for one to be charging at all times. We could also arrange to lease an extra carrier to our clients over the peak period, subject to terms, which could assist with picking speeds.
However, lets put it into context.
What happens when a forklift breaks down, or a staff member calls in sick in your current operation?
With a forklift, you will call a service engineer and wait for them to attend site. If other forklifts are available, you will probably work with a reduced output until the technician arrives and resolves the issue.
When it comes to staff, you may call upon other staff members to help out or recruit temporary workers to cope with the workloads if you expect a longer absence period.
The issue and response are very similar with an automated system.
If there is an issue, clients with an automated storage system, call a service engineer who responds immediately.
However, with the technology installed in systems such as our AUTOCUBETM Automated Racking Solution, the time it takes to get the system back online is often much quicker and more straightforward, with many issues able to be resolved remotely via Wi-fi
With fail-safe systems and opportunity charging integrated into the carriers and lifts, running out of charge is never an issue. The carriers will always return to base and charge while waiting on the next command.
If there is an issue with a carrier or lift which cannot be resolved remotely, our local service engineers will be despatched immediately to carry out on-site repairs.
So before you discount the idea of an automated storage solution because of the fear of breakdowns, contact us today and discuss the steps we take to ensure your system never experiences any downtime.
Problems with Automated Racking Systems | Automated Racking Systems Problems