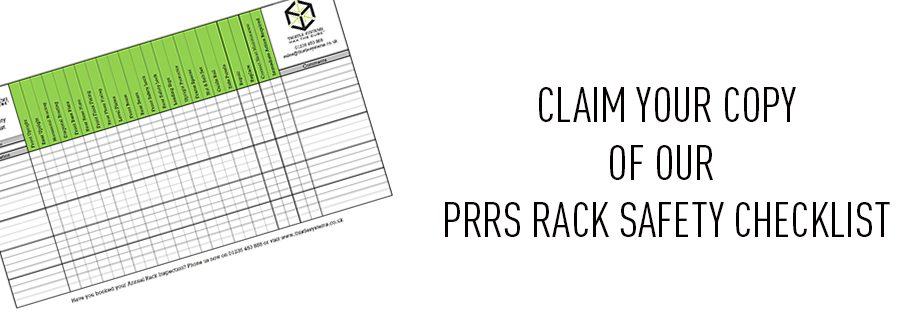
We have seen an increasing number of clients asking us about PRRS Racking Safety Training with regards to Person Responsible for Racking Safety which can only mean that this is something that the HSE are now focusing on more. Check out our PRRS Rack Safety course outline
In response to this, we have pulled together the below guidelines from the HSE to provide more of an insight into what a PRRS is and what their responsibilities include, so you can take the necessary steps to ensure you are meeting the requirements.
Racking Inspection and Maintenance
In most cases, racking is manufactured from relatively lightweight materials and therefore, there is a limit to the amount of abuse that it can endure. One factor which will have great bearing on the amount of damage likely to be caused to the racking is the skill of lift truck operators. Any damage to racking will reduce the amount of load it can handle and the greater the damage, the weaker the racking will become.
To ensure that a racking installation continues to comply with Health & Safety guidelines, the storage equipment should be inspected on a regular basis. How regularly the inspections are carried out depends on a variety of factors which are specific to each site and should be determined by a nominated ‘person responsible for racking safety’ (PRRS) to suit the operating conditions of the warehouse. This will take into consideration the frequency and method of operation as well as the dimensions of the warehouse, the equipment used and personnel involved, all of which could damage the structure. The inspection follows a hierarchical approach using several levels of inspection.
Immediate reporting
As soon as a safety problem or damage is observed by any employee, it should be reported immediately to the PRRS. You should have systems in place with regards to reporting damage and defects.
Also, employees should be provided with training, information and instruction on operating the racking system safely, including the parts affecting their safety and the safety of others.
Visual inspections
The PRRS is responsible for ensuring that inspections are made at weekly or other regular intervals based on their risk assessment. A formal written record should be kept.
‘Expert’ inspections
A technically competent person should carry out inspections at intervals of no more than 12 months. This could be a trained specialist within an organisation, a specialist from the rack supplier, or an independent qualified rack inspector. A written report should then be submitted to the PRRS with their comments and proposals for any action that is required.
Thistle Systems are currently developing a rack awareness and safety course which will provide PRRS training. If you are interested in finding out more about our PRRS Racking Safety Training, please register your interest now.
Normal rack inspections will be carried out from ground level unless there are signs of problems at a higher level that require investigation.
And while Automated and high-bay systems are less prone to damage at high level, they still require inspection and the higher levels cannot be seen from the ground. Formal inspection of these systems should include the following:
- an immediate written reporting system by the maintenance engineer who will have a daily responsibility for the system to ensure that the number and scale of any problems can be investigated by the PRRS
- an expert inspection every 12 months consisting of a minimum of 20% of the installation inspected on a rolling basis so that the complete installation is inspected every five years as a minimum requirement;
- the PRRS should carry out an appraisal of the problems found by the inspection to identify if a more extensive inspection is necessary. The racking manufacturer should be contacted for advice if there is any doubt as to the integrity of the racking system.
A record of inspections, damage and repairs should also be kept in the form of a logbook or similar.
Where damage is identified that affects the safety of the racking system, the racking should be offloaded and controls introduced to prevent it being used until remedial work has been carried out. The level of damage to the racking can be classified into 3 categories with red being serious damage, amber which is hazardous damage or green which only requires supervision.
Check out our Rack Inspection Cost Calculator to get your automatic quote
PRRS Rack Safety Training Course
If you are interested in organising training to support your PRRS, or would like to book an annual racking inspection with us, click here to contact us now or phone us on 01236 453 888.
Some of the information on this page has been taken from Warehousing and Storage: A Guide to Health and Safety by the HSE – click here to find out more