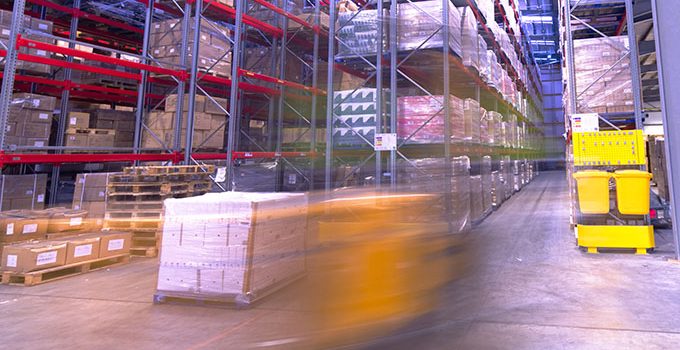
The traditional approach to warehouse design, whether it’s a new building or an extension to an existing facility, is to build the warehouse to the sizes specified by the architect or consultant based on a general rule of thumb.
Once these are agreed, the client then looks at bringing in a racking solutions company and the forklift to discuss the internal operations. Depending on the client and their position in the market, the forklifts contract may already be in place with an existing agreement with a supplier who may try to supply more of the same.
The combination of these two factors will have an enormous bearing on the racking design and the potential capacity of your warehouse and could quite literally be the difference between creating thousands of additional pallet positions and save you tens of thousands of pounds.
Unfortunately, many projects treat these factors with a silo mentality, ironically with the aim of saving money. With a little more discussion between all of the parties at an early stage, businesses could release the true potential of their warehouse.
But what is the real impact of building design and forklift specification on the racking.
1. Building Design
If the primary purpose of a warehouse facility is to store products, it is vital that you look at the racking design in tandem with the overall building design. Making the building shell marginally too small could prevent an additional bay of racking from being installed.
Whilst an extra bay of racking sounds minimal in the grand scheme of things, consider this. If each bay of racking contains 4 pallets and there are 5 beam levels, that’s 20 pallet positions. Now if there are 100 runs of pallets, that’s an extra 2000 pallet positions.
In a recent project we were called in to assist with, the client was at the early stage of the build process with the steel structure in position. However, when we looked at the drawings and began designing various racking alternatives, we quickly identified that if the design had allowed an extra 400mm in height, the client would have been able to have a racking solution which was 5 pallets high instead of 4.
This would have created over 1600 pallet positions with very limited additional cost to the actual structure, but will mean the client has to continue to use external storage for some of its products, costing tens of thousands of pounds every year.
2. Forklift Specification
The specification of the forklift will also play a major role in determining the overall capacity and efficiency of the racking solution. The first thing the forklift specification will impact on is the required aisle width between the racking uprights.
So for example, using existing forklifts which are design to suit standard adjustable pallet racking will immediately prevent the specification of narrow aisle racking and potentially drive in. The physical reach of the forklift will also determine how high the racking can go. A forklift with a reach of 3 metres will clearly be unable to place a pallet on a beam which is 4 metres high.
By designing the racking in conjunction with the specification of the forklift will allow you to explore the full range of alternatives to maximise the cube.
Conclusion
Every project has its limitations and constraints but the secret to successful project management is to attempt to remove as many as possible prior to the start date.
By working with Thistle Systems at the earliest stage possible, we can assist you to max your cube by providing you with the optimum design which looks to maximise the capacity in the smallest footprint whilst minimising the long terms costs.
By understanding your SKUs, stock movements and products being stored we can work with all the partners involved in the project to deliver the most effective solution.
To find out more and to discuss your project, contact us now on 01236 453888.