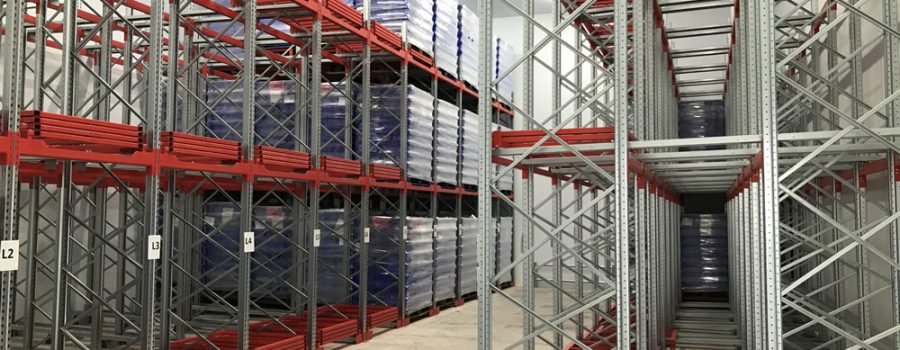
The Push back racking system is probably one of the most flexible dynamic pallet racking solutions on the market today. Not only can it deliver high-density storage solutions, but our Maxi Cube Push Back Racking can also dramatically improve picking speeds and space utilisation, which can significantly reduce operational costs.
Below, we explain a few of the more typical uses for a push back racking system or check out the video below.
Creating High Density Storage with Push Back Pallet Racking Systems
Space is at a premium in most warehouses and so many smart companies are looking at how they can maximise storage capacity in the smallest area possible to reduce the average storage cost per pallet.
Push back racking’s ability to store up to 6 pallets deep can enable companies to create blocks of high density storage in a fraction of the space required by adjustable pallet racking.
It is most suited to warehouses where multiple pallets of SKUs are being stored and where 100% accessibility is not essential. That being said, the retrieval and loading time of pallets to and from push back racking is extremely efficient, thanks to the gravity fed carts.
Push Back Racking is also an effective solution for safely storing IBCs. As warehouses are often reluctant to store any more than two high due to health and safety concerns, a push back racking system can use the available height to create a storage solution which maximises capacity while reducing the floor space required.
Doubling Capacity with a Double Deep Push Back Racking System
Sometimes you just need an extra run of racking to provide you with all the capacity you need. And whether you are looking to double the capacity of your single run of racking against a wall of the warehouse or looking to double up on one run in a wider aisle, double deep racking can often be the answer.
Traditional double deep racking typically requires alterations to be made to the forklift to increase the length of the forks, allowing the pallet to be positioned at the rear position.
However, push back racking can provide the double deep system without any alterations by using its gravity-fed cart approach to access the rear pallet.
Push Back Racking Systems for Cold Stores
Push back racking is becoming increasingly popular for companies which rely on cold stores. With running costs high to keep the products chilled, it is vital that you have a storage solution which maximises capacity and space utilisation.
Storing up to 6 pallets deep, push back racking can provide a high density storage solution which can outperform most racking systems for cold stores.
However, it is the space utilisation benefit which is seeing many companies switch from the traditionally popular drive in racking to push back racking. The cart system enables the fork lift operator to retrieve pallets from any picking face and access any level without having to completely remove an entire bay.
Push Back Racking Systems for Despatch Bays
Despatch bays can be very busy areas with forklifts trying to load wagons as quickly as they can to minimise the waiting time.
Companies have tried to minimise the loading time by creating marshalling areas where pallets are placed ready to be loaded directly onto the wagon.
But with typical HGVs capable of accommodating as much as 26-30 pallets, depending on the size of the pallets, this can require a significant amount of floor space.
By creating a push back racking system which is 3 pallets high by 2 wide and 5 deep, companies can store an entire load in 66% less floor space – as well as reducing travel times for picking and loading.
Click here to find out more about our Maxi Cube Push Back Racking or contact us now to discuss your warehouse.