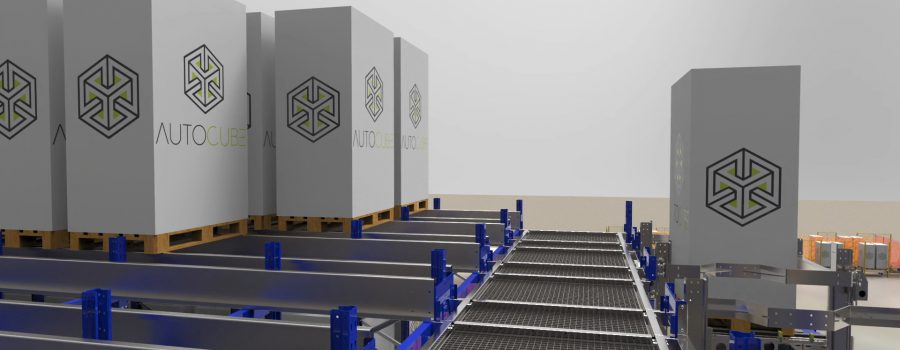
AUTOMATED RACKING MYTH BUSTING NUMBER 1:
Most people accept and understand the general concept of automated racking systems and the significant operational benefits it can deliver.
However, there is a general misconception that automated racking and storage are only suitable for larger warehouses and cold stores.
The truth is the viable size of automated storage isn’t down to the number of pallet positions. It is actually down to a number of factors including, the available space, the number of SKUs, the picking process, and the required throughput of the operations.
But possibly most importantly, it is also down to the mindset and the business philosophy of the company.
A traditional approach will usually consider forklifts and manual racking solutions as the trusted modus operandi and accept the multitude of ongoing operational costs, risks, and potential fluctuations of productivity and profitability – because that is the way it has always been done.
A progressive and systematic mindset with a focus on the data will look at the repetitive nature of the tasks being carried out, seek to eliminate the risks involved and look to determine the most cost-effective solution.
So an automated storage solution may be able to increase capacity in a large warehouse to deliver an additional 40% in storage capacity and reduce the number of forklift trucks and operators by over 60%, therefore delivering significant savings and a relatively short return on investment period.
However, it is equally viable in a smaller warehouse which only requires a storage capacity of 300 or 600 pallets, with a relatively low number of SKUs but where space is at an absolute premium with a very high velocity of stock throughput.
The number of operators required to facilitate the throughput is such that to use a manual approach would require significantly more space and significantly more forklifts and operators, therefore driving up ongoing costs.
Similarly, the automated approach was seen to be the optimum solution in a cold storage facility with only 300 pallets using 2 lifts and 3 smart carriers to store and retrieve the pallets from the system without the need for manual handling.
The facility was operating 24 hours per day and required a throughput of over 60 pallets per hour.By reducing the floorspace of the cold store, they were able to minimise the running costs of the cold store and by going fully automated, they were able to avoid the safety issues and reduce the energy costs from personnel going in and out of the facility. We can also design the system around an ambient inbound and outbound zone avoiding coldstore procedures for your associates.
So before you believe the automated racking myths that it is only viable for large warehouses, maybe its worth investigating further.
Give us a call on 01236 453888 or contact us now to discuss your requirements
Automated Racking Myths | Automated Racking Explained