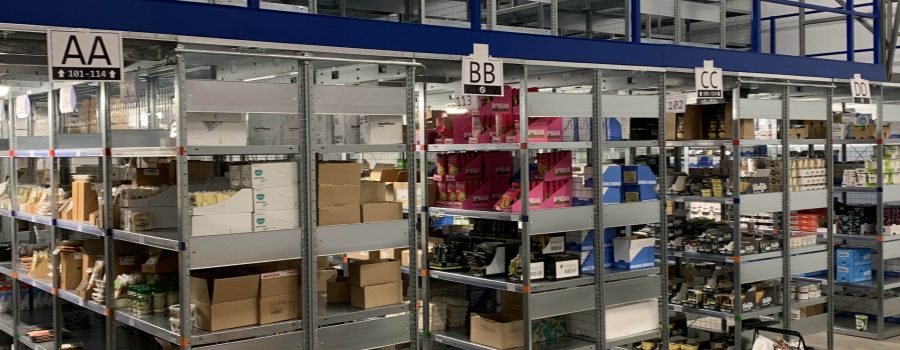
The exponential growth of SKUs is a challenge facing many warehouse managers and none more so than those operating within the wholesale market.
The challenge is further compounded by customers looking for greater flexibility in ordering, resulting in more mixed pallets being created and, as a result, more broken/split/half pallets needing to be stored.
The traditional approach in the wholesale market has been to store everything on pallet racking or narrow aisle racking. This gives 100% accessibility to all products with faster moving SKUs located at lower levels to maximise picking speeds for these key products.
The simple answer to creating more pallet positions in the same space whilst providing 100% accessibility has traditionally been to move from pallet racking to narrow aisle racking or very narrow aisle racking.
However, this doesn’t address some of the underlying issues, particularly when it comes to split and part pallets.
The major challenge of split pallets is that it creates a massive space utilisation issue. If you walk into any wholesale warehouse, you will see clear evidence for yourself with large empty spaces between products on one beam level and those on the next beam level.
Some companies have introduced timber decking to the racking with additional beam levels to create shelving areas which can improve some space utilisation and allow more low volume SKUs to be stored on a beam level.
However, in many cases, the cubic space issue is simply moved to the depth of the shelving instead of the height of the pallet racking.
Other challenges are also presented, including the heights for picking and the safety issues of having pickers and forklift trucks operating in the same environment.
Time for a New Approach to Warehouse Design
The key challenges facing many companies at the moment included:
- The need to increase storage capacity
- The need to store more SKUs
- The need to improve picking speeds and efficiency
- The inefficiency of storing half pallets on static pallet racking
- Space utilisation
- Slow picking speeds
- The safety issues of a busy warehouse with picking staff and FLTs in the same are
This demands a fresh approach focused on a better understanding of your stock profile, stock turnover and picking speeds.
Only once you understand the new stock profile, are you able to design an efficient warehouse storage solution that will truly maximise capacity and dramatically reduce operating costs using a combination of storage solutions to suit the different SKUs being stored.
Thistle Systems has developed its unique Max the Cube™ approach which draws upon tens of thousands of hours in design, analysis and training to develop a proven method of designing warehouse solutions for the modern environment.
Contact Thistle Systems to discuss your warehouse requirements now.