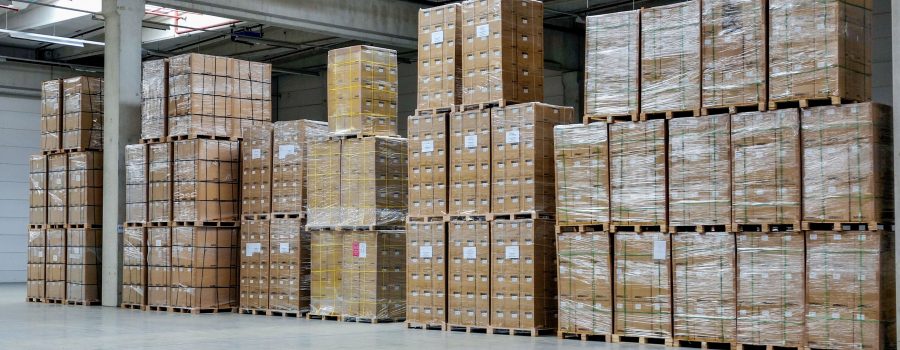
Block stacking in your warehouse is generally perceived as the cheapest approach to storing your products, and you would be forgiven for agreeing.
Yes, it requires zero investment in racking systems, and the only piece of equipment needed is a forklift truck.
However, many smart companies focused on safety are recognising what is perceived as the “cheapest approach” in block stacking may not be the most effective approach – and in fact, it may be costing them money.
That’s because more companies are recognising the issues of space utilisation and extreme inefficiencies of block stacking their products in a warehouse when compared to a semi-automated storage solution such as shuttle racking.
So here are a few issues which you should consider if you are block stacking.
Storage Capacity
One of the primary measures of any storage solution in a warehouse is the maximum number of pallets which can physically be stored in the available space.
The potential storage capacity of the block stacking approach is, in theory, high. With no uprights are beams, you may think you are only limited by the height of the building and the number of pallets you are prepared to stack on top of each other.
However, aisles still need to be created to allow forklift movements which will reduce the storage space. The more forklifts you require to meeting your picking demands, the bigger the aisle widths need to be.
The height of block stacking is limited by the types of products stored and the likelihood they will be damaged. Any damage to products being block stacked represents a significant health and safety risk with collapses a real threat of injury to employees.
The HSE is tightening up its measures and guidelines to limit the number of pallets you can safely stack on top of each other, severely impacting the storage capacity, which can be achieved.
Space Utilisation
Whilst potential capacity may be relatively high, actual space utilisation in a block stacked warehouse tends to be much lower.
The use of stows to manage SKUs severely limits space utilisation – especially when the stow can be up to 10 pallets deep in some warehouses.
The utilisation diminishes each time a pallet is picked as the system does not allow the SKU capacity to be replenished.
Many operators of warehouses with block stacked pallets spend a significant amount of time simply moving pallets to improve space utilisation – at significant cost when you take into consideration the labour and forklift costs.
Picking Speeds
Picking speeds in a blocked stacked warehouse tends to be significantly slower than other forms of storage systems.
This may be because it can be more challenging to remove pallets from a stow than a racking system carefully, and the layout of the warehouse may often be a little irregular causing travel times to be much slower.
Additional Forklifts
Many companies have seen the need to increase the number of forklifts in an effort to offset the slow picking speeds to meet the increasing demands on the warehouse.
This has seen a direct increase in the operating costs of the warehouse when you take into consideration the additional costs which include
- Leasing costs of forklifts
- Labour costs (including recruitment, training, holiday, sickness, absenteeism)
- Energy/Fuel Costs
- Servicing costs
Third Party Storage Costs
A key symptom of block storage not meeting a company’s storage requirements is the ongoing reliance on third party storage to provide the additional capacity needed.
The bottom line is if you are using third party storage, you may be incurring additional and unnecessary costs for zero long term benefits.
By investing these monies in a more effective and efficient storage system, you could deliver significant long term benefits.
Why You Should Consider Semi-Automated Storage Solutions As Opposed to Block Stacking
Semi-automated and fully automated storage solutions can deliver significant benefits over block stacking by eliminating many of the hidden costs and delivering a highly attractive return on investment. These include:
- Increasing capacity by as much as 100-200%
- Improving space utilisation
- Eliminating third party storage
- Reducing forklift requirements
- Reducing labour costs
- Improving picking speeds
- Reducing damage to products
- Improving safety in the warehouse
Click here to find out more about our Semi-Automated Storage solution
Or Discover the benefits of moving to a fully automated racking system
Block Stacking Warehouse | Cheapest Warehouse Storage Solution | Automated Racking System