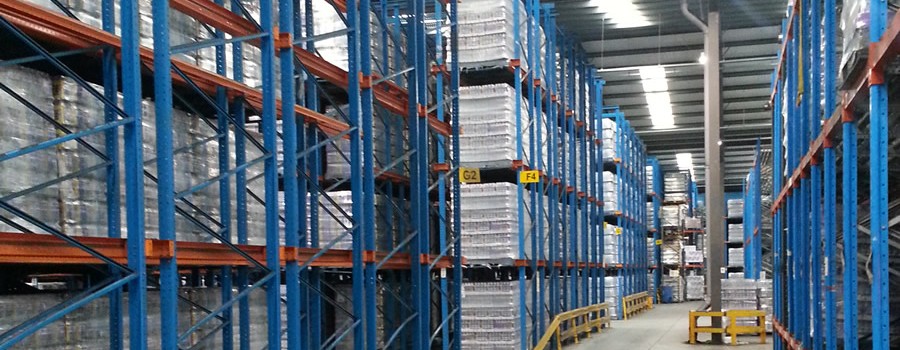
As more companies look for ways in which they can make savings, Thistle Systems Group, one of the UK’s leading suppliers of racking has urged all companies to think carefully about the potential dangers of purchasing and installing used racking systems.
With offers of amazing savings from online retailers and auction sites such as ebay as well as a few less scrupulous racking suppliers, there is plenty of temptation for businesses who are looking to increase their storage capacity on a budget with used racking.
However whilst some second hand racking may look of good quality, it is virtually impossible to guarantee that it is fit for purpose without full knowledge of what it had been designed to do in the first instance.
You would also need proof that the previous ‘owners’ of the racking will have carried out regular inspections, carried out any necessary repairs and replace damaged components to ensure it is kept in a safe condition.
The equipment may appear free from physical damage however it is extremely difficult to identify what level of degradation has taken place which would result in the equipment not being capable of carrying the same load levels as new components.
The degradation can be caused by overloading, fire damage, use in cold stores, internal corrosion. And most will be invisible to the naked eye.
At the most basic level, you could be opening yourself to risk by buying equipment which has been incorrectly identified and specified. To carry this out with absolute certainty would require detailed data and experience to ensure that the racking supplied will safely carry the loads required in the new configuration.
In addition, further problems can be caused by components being modified such as beams cut and re-welded, or frames incorrectly braced, cut or joined by a previous user, or your second hand supplier, to make them fit their required installation.
These modifications will have a major effect on the load capacity and safety implications.
Thistle’s Managing Director, Mike Cairns, said “The fact of the matter is that racking is legally classed as work equipment and is therefore, covered by The Provision and Use of Work Equipment Regulations 1998 (PUWER 1998) which states that employers have a responsibility to ensure that the work equipment they provide is safe to use and fit for purpose.”
He continued, “This means that in the event that an accident occurs in your workplace and it is found that you have purchased and installed equipment which you cannot demonstrate is safe to use and fit for purpose, the Company Directors can be held personally responsible – ultimately with jail sentences.”
Thistle has also warned second hand packages are also more than likely to be supplied with accessories from mixed manufacturers and whilst each may be sound in their own right, may not be covered by any guarantee when used together.
And when it comes to the installation of used racking purchased from a separate source whether it is online or from a used racking supplier, Thistle warn that there are further issues that must be taken into consideration to ensure that you are meeting the very basic levels of health and safety requirements
Mike explained, “Firstly you need to ensure that only approved and knowledgeable people were used to dismantle, transport and store the racking to ensure that no damage occurred during this critical process.”
He continued “Secondly the rebuild should ideally be exactly as the original installation or that sufficient data is available for qualified people to confirm that the components will be capable of being used safely in the new design and that the re-erection is carried out in accordance with SEMA codes and using SEIRS registered installers.”
A key issue that most companies purchasing second hand racking will face is that of load notice, a legal requirement under the health and safety guidelines
Mike added, “It would be extremely difficult for any reputable company to issue load notices to put on the used racking system unless they have full access to critical design information, product data and inspection reports. It is for this very reason that we have turned down every request for us to either supply or install second hand racking.”
So if you are considering second hand racking as an option for your business it is vital that you weigh up the short term cost savings against the potential consequences of sub standard racking.