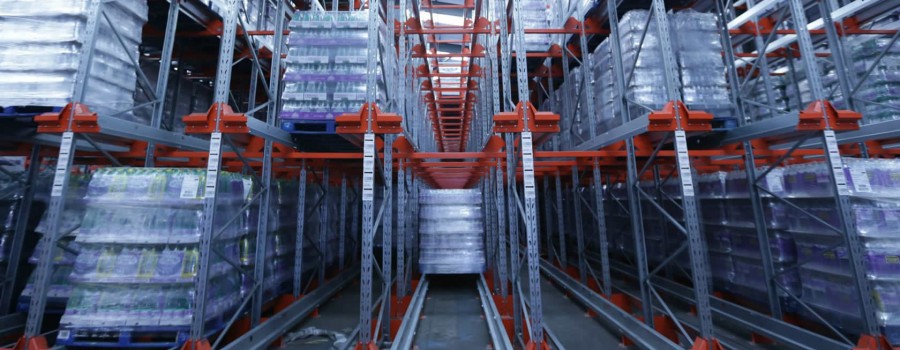
Looking for the best warehouse racking system to maximise capacity and improve the performance of your warehouse?
It’s a question that we are often asked but unfortunately, there isn’t one simple answer.
The footprint and height of each warehouse may be slightly different. The pallet size may vary. The products being stored are likely to be different.
However, the real secret to achieving the best warehouse racking system is understanding the volume and movement of products in the warehouse and designing a racking system which optimises the flow of products and traffic.
This could be combining a radio shuttle solution to handle the core storage requirements with pallet live racking to optimise the despatch area.
It could be standard adjustable racking to enable 100% accessibility of products in the warehouse with push back racking to maximise capacity for packaging materials.
It even applies to shelving where heavy duty shelving can be used to maximise capacity and a carton live system to transform the picking speed.
Failure to understand the demands on the system will inevitably lead the design of the racking failing to deliver.
This failure could be a failure to maximise capacity and therefore require offsite storage or a compromise to the service you can offer to clients. It could mean a slow picking system which impacts of loading times. It could result requiring additional labour. And in some cases, you could have to sacrifice valuable production space to ensure you have the necessary storage capacity.
It’s this awareness which separates a sales orientated racking company from a solutions focused company, like Thistle Systems.
We help companies across the UK to deliver solutions which maximise capacity and, most importantly, improve operational efficiency and dramatically reduce costs.
To find out more about our range of warehouse racking solutions and find the best warehouse racking system for you, click here