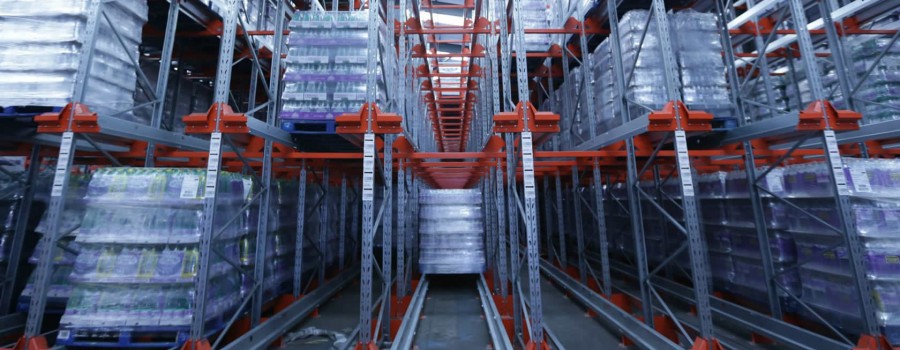
Have you considered how much money you spend every year stocking and retrieving pallets from your warehouse?
The cost of forklift trucks and drivers is a sizable element of any warehouse operation but is often overlooked when deciding on the optimum racking solution.
And whilst drive-in racking is seen by many companies as an excellent high-density solution, they often discover it doesn’t suit fast-moving warehouses that need to access pallets quickly.
It was certainly the case when we spoke to a large manufacturer in the food and drink sector when we were asked to quote an extension to their existing drive-in racking solution to help improve capacity in their warehouse facility.
After carrying out a site survey and looking at the best drive-in racking design, we used a computer simulation to demonstrate the average travel time required for a forklift could cause issues to meet the demands of their distribution network.
This was an area that was already causing the company some concern, and they could not afford to further exacerbate this.
We proposed an alternative solution to their warehouse design which featured a shuttle racking system which not only reduced their estimated travel times by approximately 56%, and we were also able to increase the storage capacity by 44% within the same footprint.
By dramatically reducing the travel times, the solution enabled the company to review the number of forklifts required in the warehouse.
As a direct consequence, the company could also review the staffing levels and redeploy resources to other areas in the business.
Check out our blog “The 5 Reasons Why Companies Are Switching from Drive-In to Shuttle Racking”
To find out more, contact us now on 01236 453888 or check out our shuttle racking solutions.