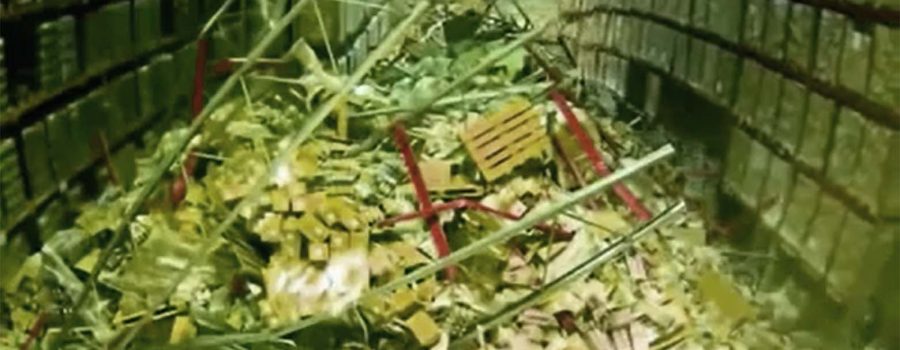
There is incredible video footage shows the devastating impact poorly constructed racking can have on a warehouse.
The most worrying aspect is how little contact there is between the forklift and the horizontal beam which causes virtually all of the racking to collapse.
It’s almost impossible to determine the real cause of the problem from the video, however we would suggest its most likely to be down to the quality of installation and the bracing of the uprights. If you look closely, you can see the system is missing bracing on one of the sections and features a horizontal bracing bar incorrectly locate about 1 metre off the ground (and holding jackets). It is unclear whether there is another horizontal bracing bar at the bottom of the racking.
The good news is that by taking some simple steps, you can greatly minimise the risk of potential incidents.
1. Ensure Your Racking Is Installed Correctly
Racking should only ever be installed by an experienced racking installer to ensure it is structurally sounds and complies with the latest health and safety regulations. This ensures is constructed correctly, with the correct fixings, to the right tolerances and with the right bracing pattern – all of which are key to providing the necessary load capacity and strength.
2. Know Your Racking and Its Limitations
One of the most important factors that will impact on the safety of your racking, will be the type and origin of your racking itself.
As a minimum any racking being used in the UK must comply with the latest SEMA standards, however we would recommend that companies should be looking for racking that meets the new European Norm, which offers a great level of safety standards.
Every racking installation should have loading signs clearly displayed, showing the maximum load capacities and any potential limitations. Failure to have loading signs is in breach of the health and safety guidelines and could result in a fine.
Over the years, many manufactures have supplied their own particular design of racking, however a number are no longer. Whilst this may appear to be a rather trivial matter, it could mean costly repairs should replacement parts be required.
3. Avoid Using Second Hand Racking
Second hand racking is seen by many companies as a cost effective solution to a problem and with the number of companies going out of business, there is a growing amount available.
But the major problem with second hand racking is unless you have complete knowledge of how and where it was used previously, you can never truly be confident of its actual condition. Previous damage can be concealed by new paint. Internal defects caused by the environment could remain undiscovered until it’s too late and before you know it, the supposed cost effective solution could be costing you far more than you ever expected.
Click here for our full article on new vs second hand racking.
4. Invest in Quality Rack Protection
Racking protection is often seen by companies either as a necessary evil or even as just an accessory which would be nice to have but not essential – especially when budgets are tight. Sadly this couldn’t be further from the truth.
Adequate rack protection can not only protect your investment in the racking and minimise repair costs but it can also minimise the risk of the racking collapsing and potential injury to employees.
Click here to find out more about the benefits of rack protection
5. Avoid Performing Unauthorised Rack Alterations In House
Whilst change is inevitable in any business, the temptation to alter your racking without consulting with the manufacturer or at the very least a trained installer could have catastrophic effects.
For example, raising the beam level within your racking could potentially reduce your load capacity by as much as 80%.
Whilst it’s always recommended to have racking installed and altered by SEIRS accredited installers, a quick call to the supplier prior to any changes in the current layout could prevent major issues and incidents.
Click here to find out more about the dangers of amending racking in house.
6. Carry Out Weekly Racking Inspections
The old adage about prevention is better than a cure is never truer in racking.
There is, of course, a legal requirement on every organisation to ensure they provide a safe working environment for their staff and as part of this, companies are required to carry out an annual inspection of their racking system and address any issues.
However, by carrying out more regular visual inspections daily or weekly by your own employees could not only identify potential defects before they become serious issues, it could also save thousands of pounds. The good news is that it needn’t take long and requires only a basic understanding of racking safety to make a major difference.
7. Get the Right Design Advice for Your Racking System
As with most safety issues, the level of risk presented by your racking can be minimised by getting the right level of design advice and experience. The use of anti-collapse mesh panels, rack protection, traffic management and sufficient aisle space can assist with safety in the warehouse.
However, using advanced design systems such as our Max the Cube philosophy which looks to maximise the capacity in the available space, maximising the safety and minimising the lifetime cost of the racking can offer significant benefits.
For example, by using radio shuttles instead of drive in racking you can increase capacity and minimise the amount of contact the fork lift truck with the racking system and therefore minimising the likelihood of damage to uprights. By looking at creating picking tunnels with buffer stocks above you can minimise the risk of accidents with fork lifts whilst creating a more efficient picking system.
By taking a more holistic approach to the design phase, you can not only Maximise the Capacity and improve the efficiency of your warehouse, you can also improve safety and reduce costs.